|
|
|
|
|
Renovation and construcion machinery |
|
In the renovation and construction of machinery we do mostly
electric - electronic engineering: reconstruction and installation
of processor management, automation, modernization of
drive components. Together with outside engineering partners
we can also execute complex reconstruction or build new machinery.
|
|
|
|
|
|
|
General approaches to the
renovation and construction of machinery
We invest our knowledge and experience in the optimal solution of tasks
in the areas of electric motor
drive system, motion control, industrial
automation and industrial
electronics, and
link them with experience, technological needs and skills of customers.
Our guidance is providing integrated
solutions. At planning the realization
we use the newest equipment and solutions, with special emphasis on the
demands of safety regarding machinery. For this purpose we have established
our own booklet of standards in the field of electrical equipment and
machinery safety.
Our reference contains
many examples of solutions in areas of reconstruction and
building of machinery in various industries. Some
successful solutions are described in detail in the publications
and articles.
|
|
|
|
Some (special) examples
of designed solutions
A set for microprocessor control of spot welding machines
Automatic TIG welding
|
|
|
|
A set for microprocessor
control of spot welding machines
The kit is designed to upgrade –replace the steering regulating
part of machines for spot welding, for machinery of power ratings up
to 48 kVA @ 400V.
It contains a processor unit with the power supply unit and a module
for adjustment, display and thyristor controlled voltage source.
The kit is in an embedded shape. With it we can replace the ignition
contaktor and the rest of the steering machine.
The main advantages of the system:
- thyristor control allows federal and optional settings
of the welding current (by adjusting the primary voltage
of the welding transformer), in both time and shape;
- synchronization of the thyristor control with the power
supply also allows the realization of extremely short and
strong welding pulses for the best possible quality of
welds from stainless sheet
- Processor support of the system (full digital implementation)
enables accurate and reproducible setting of welding parameters:
- time before the start of welding
- start, intermediate and final welding current, together with the
times
- time at the end of welding
- the time between the two welds in serial welding
- choice between individual and serial welding
- the parameters that describe the welding are grouped
into predefined items and stored in the memory of the machine;
the user easily selects the items, but it is not necessary
to know the welding parameters, if not desired.
|
|
|
|
Automatic
TIG welding
The equipment set is designed for installation to the mechanics of single-axle
welding machines
manufactured by AVP Ljubljana or similar.
The contents of the set:
- programmable logic controllers (24 dig. inputs, 16 dig.
outputs, 5 analog inputs, 2 analog outputs) with the appropriate
software and integrated
- positioning system (actuator: asynhronic motor with a
built-in incremental encoder and helix, frequency inverter,
reference switch)
- user panel for setting the process parameters and control
- visualization of events in the machine
- interface for control of the welding source
- installation on the machine and system start-up
The set is designed for automatic control of the longitudinal welding.
The main advantages of the solution:
- the system is designed so that the largest possible part
of the welding works automatically, without the activity
of the user. The user should only clamp the workpiece,
the machine itself then finds the beginning of the plate,
carries out the welding, ends the weld, finds the next
piece (a total of up to 3), repeats the cycle, ...
- the whole digital implementation of the system (command
of movements and welding) assures the constancy of welding
parameters and thus reproducible assurance of product quality.
- the settings of welding parameters are stored in the
memory devices in the form of products. Individual products
contain all the necessary settings to ensure the quality
of the welding:
- shifts of the welding head:
- speed of the search of plates
- time of the pre-blow
- accelerating time after welding ignition
- welding speed
- time of the after-blow
- welding parameters (in relation to the source of
the welding):
- the way of welding
- time format of the welding current (height and times)
- the rest of the time parameters
- Such an approach allows a maximum simplified work to
the user of the device: he/she only has to select the correct
item, clamp workpiece and start welding.
|
|
|
|
|
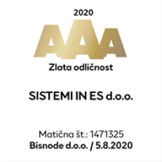
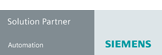
|
|
|
|
|